As the largest producer and user of lithium ion batteries, China dominates the global battery supply chain, including the emerging industry of recycling.
In 2025, China is forecast to account for 78% of battery pre-treatment capacity and 89% of black mass refining capacity, as assessed by Rho Motion’s Battery Recycling Forecast.
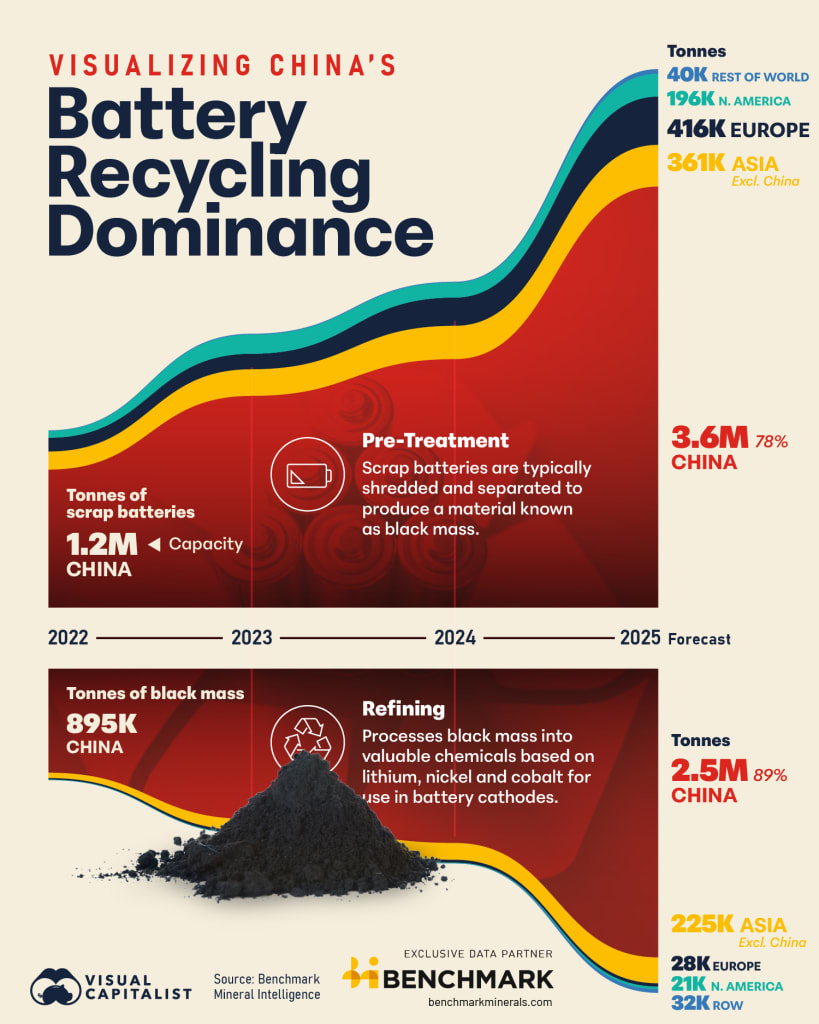
How are batteries recycled?
The first stage of the battery recycling process is the collection of scrap from battery production facilities or end-of-life batteries. Given that China has the largest electric vehicle market and is forecast to account for 85% of 2025 battery production, China’s recycling industry has ready access to substantial volumes of feedstock.
The collected scrap is then pre-treated, typically through a mechanical shredding process, to produce a material known as black mass. This material contains lithium, nickel, cobalt and other valuable battery minerals.
Outside of China, pre-treatment is the stage for which many regions have primarily built capacity. For example, of the 38 operational recycling assets in Europe, 28 focus on pre-treatment only.
The black mass is then refined into chemicals for use in the production of new battery cathode materials. Some refiners convert black mass directly into pre-cathode active material (pCAM), whereas others produce chemicals that may need further refining before they are ready to be used in CAM or pCAM production processes.
China and South Korea both have large overcapacities of refining capacity, meaning they must source feedstock from other regions such as Europe and North America which have a deficit of refining capacity.
More Information
This infographic is based on data from our Battery Recycling Forecast, which provides a long-term outlook for global feedstocks available for recycling by region, battery chemistry and feedstock covering end-of-life EVs, BESS, portables and 2 & 3 wheelers and production scrap.
To find out more, click here.