Lithium-ion battery recycling is an essential and rapidly evolving process aimed at recovering valuable materials from used batteries, particularly those used in electric vehicles (EVs), consumer electronics, and energy storage systems. As the demand for lithium-ion batteries rises, driven by the transition to electric mobility and renewable energy solutions, sustainable management of these batteries throughout their lifecycle has become increasingly important. Recycling lithium-ion batteries addresses environmental concerns related to battery waste, such as the leakage of toxic chemicals and heavy metals, and facilitates the recovery of critical materials like lithium, cobalt, nickel, and manganese. These resources are finite and costly to extract, making their recovery through recycling economically advantageous and strategically significant. Ultimately, lithium-ion battery recycling is vital for promoting a circular economy, where materials are continuously reused, reducing reliance on raw material extraction and supporting a more sustainable battery supply chain for future generations.

How has demand for recycling grown?
The demand for lithium-ion battery recycling is projected to grow significantly, largely driven by the rising adoption of EVs and expanding battery production. By 2030, the global EV market is expected to expand considerably, resulting in millions of vehicles reaching the end of their operational lives and necessitating enhanced recycling efforts to reclaim valuable materials like lithium, cobalt, and nickel. Furthermore, as supply chain challenges and sustainability goals become increasingly prominent, manufacturers are focusing on incorporating recycled content into their products, which will further drive the demand for recycled materials in battery production.
Forecasts indicate that the demand for feedstock in lithium-ion battery recycling will surpass 0.9 TWh by 2030, with the automotive sector being a significant contributor. To meet this increasing need, efficient collection and recycling systems must be developed to manage both post-consumer batteries and pre-consumer feedstocks, such as production scrap from battery manufacturing facilities. These advancements are critical for ensuring a sustainable supply chain within the battery recycling industry.
What has driven capacity development regionally?
The global battery recycling capacity is steadily increasing in response to the growing volume of used lithium-ion batteries, with Rho Motion forecasting it will exceed 1.2 million metric tons by 2030. This expansion is essential to accommodate the influx of end-of-life batteries from the EV sector, which is expected to continue its upward trajectory in the coming years.
The development of lithium-ion battery recycling infrastructure varies significantly across regions, with notable efforts underway in China, Europe, North America, and other notable markets such as South Korea and India.
China currently leads the global battery recycling market, driven predominantly by its extensive EV industry, manufacturing capabilities, and supportive government policies. Major recycling firms are scaling up operations to manage the increasing volume of EoL batteries and production scrap.
In Europe, recycling infrastructure has evolved mainly as a response to regulations such as the EU Battery Regulation and the Critical Raw Materials Act (CRMA). The Battery Regulation replaced the previous battery direct and aims to regulate the entire lifecycle of batteries within the EU to reduce environmental impacts, improve sustainability, and support a circular economy. While the CRMA addresses the EU’s dependence on imported raw materials which includes battery raw materials, in this it supports the development of a battery recycling industry. These regulations enforce recycling targets and mandate the use of recycled materials in new batteries. Recyclers are establishing large recycling facilities across the continent to create a closed loop on critical materials.
Capacity growth in North America initially developed slower than in Europe or China. However, with the arrival of the Biden Administration Inflation Reduction Act (IRA) and Department of Energy (DOE) support, funding into the battery recycling sector has increased hugely, initiating investments into the recycling industry. Capacity development in the sector has largely been led by federal funding. While the IRA looks set to be cancelled under President Trump, the IRA has succeeded in supporting the industry through its infancy.
South Korea has one of the most developed recycling markets. This capacity expansion has been driven through market led growth with larger conglomerate companies investing into the emerging battery recycling sector, these investments have been supported by the links South Korea has to the wider battery industry with players such as Samsung SDI, LG Energy solution and SK innovation all based there, as well as the general ease at which players can establish facilities.
India is a market that is showing signs of growth in the battery recycling sector. Largely this is through its 2023 Battery Waste Management (BWM) Rules which prioritises collection and recycling to address its growing e-waste and EoL batteries. Differing to China, Europe and North America the majority of the country’s batteries are in the 2/3-wheeler segments with a limited number of electric cars and larger vehicles. The country also has limited government backed subsidies and incentives directed towards developing a domestic recycling industry.
Development on smaller scales is also occurring in African countries, as they look to deal with the increasing volume of e-waster and batteries.
Collectively, these global efforts signify a clear movement toward sustainable battery supply chains, as each region seeks to enhance access to critical materials while minimising environmental impact.
The battery recycling process
The recycling process for lithium-ion batteries is complex and involves several stages to ensure the efficient recovery of valuable materials. The typical process includes:
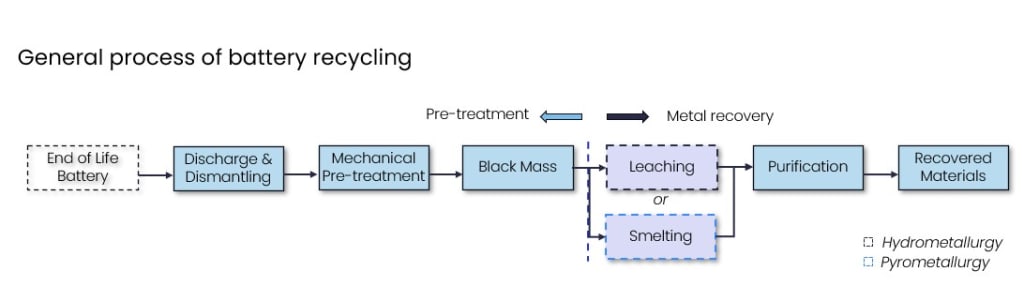
1. Collection of EoL batteries
Batteries from manufacturing gigafactories, EVs, consumer electronics, and industrial applications are collected once they reach the end of their lifecycle.
2. Dismantling the battery pack
After collection, the battery pack is disassembled to separate individual battery cells, which are assessed for their potential for reuse or the need for full recycling.
3. Battery cell disassembly
Cells that cannot be reused are mechanically or chemically broken down, resulting in a coarse mixture known as “black mass,” which contains various metals, including lithium, nickel, and cobalt.
4. Production of black mass
Black mass serves as a crucial intermediate product in the battery recycling process. Following dismantling and shredding, it represents a mixture of active metals ready for further refinement. This black mass is processed to separate valuable materials.
5. Conversion to metal salts or other recovered materials
The black mass undergoes chemical treatments to separate and refine metals, often converting them into salts like lithium carbonate or nickel sulphate. These materials are then prepared for reuse in new batteries or other industrial applications, completing the recycling cycle.
What technology is used in battery recycling?
The lithium-ion battery recycling market employs various technologies, each with distinct advantages and limitations tailored to specific applications. Effective material recovery typically involves two primary stages: pre-treatment and black mass refining.
- Pre-treatment to produce black mass
In the pre-treatment phase, batteries are shredded or crushed into a coarse material known as “black mass,” which contains a mix of valuable metals like lithium, cobalt, and nickel. This stage may include additional processes, such as thermal pre-treatment, which applies controlled heat to facilitate handling, or solvent washing to eliminate impurities. These preparatory steps enhance the efficiency of metal extraction in the subsequent stage.
2. Black mass refining to produce battery materials
In the refining stage, the black mass undergoes chemical processing using solvents and acids to separate individual metals. Once isolated, these metals are refined and purified into usable forms, such as lithium carbonate or nickel sulphate, suitable for direct use in manufacturing new battery components. This stage is crucial for producing high-purity materials that meet specifications for battery production, enabling recycled metals to re-enter the battery supply chain as quality resources.
Within the industry battery recycling is achieved using three primary methods: pyrometallurgy, hydrometallurgy, and direct recycling, each with unique processes, benefits, and challenges.
Hydrometallurgy relies on leaching agents, ranging from inorganic acids to biological solutions, to dissolve metals into a recoverable form, its recovery rate can reach up to 98% for copper, nickel, and lithium. The process begins with shredding or crushing batteries into smaller components, separating valuable substances into a “black mass” rich in critical metals like cobalt, nickel, and manganese. This black mass is further refined to produce high-purity, battery-grade materials capable of re-entering the supply chain. Hydrometallurgy has a lower carbon footprint and requires less energy than pyrometallurgy, making it a more environmentally friendly choice. However, its reliance on hazardous chemicals introduces challenges, including the release of volatile organic compounds and risks of wastewater contamination. Companies employing this method often invest in wastewater treatment systems to mitigate these risks, although variability in battery chemistries and sizes still complicates large-scale adoption.
Pyrometallurgy employs high temperatures to extract and purify metals from end-of-life batteries. It generally begins with thermal treatment at 140°C to 500°C to remove volatile substances such as electrolytes and solvents, followed by smelting at 1400°C to 1700°C, producing cobalt, copper, and nickel alloys alongside a slag containing lithium and aluminium oxides. While this method is efficient at processing mixed waste streams and operates with comparably simple steps and faster reaction times, it is adopted less nowadays as traditionally it demands substantial energy and emits significant amounts of carbon dioxide and toxic gases. Additionally, the process can result in the loss of some recoverable critical materials such as lithium during combustion or smelting. However, companies are countering these drawbacks altering the traditional pyrometallurgy process to improve material recovery rates, the energy consumption and carbon footprint of the process. Additionally, some companies employ a dual strategy using both pyrometallurgy and hydrometallurgy to capitalise on the advantages of each process.
Direct recycling is the most energy-efficient and environmentally benign method, focusing on preserving the functional structure of battery components. This process involves physically disassembling batteries to recover key materials such as cathodes and anodes, with an emphasis on maintaining their integrity. Supplementing lithium-deficient cathodes or regenerating anodes enables their reuse in new batteries without significant degradation in performance. The process reduces energy consumption and downstream processing while yielding high-quality, impurity-free materials. Despite its advantages, direct recycling remains technologically immature, with scalability hindered by labour-intensive procedures and the absence of a well-established commercial framework. Overcoming these limitations is essential to unlock its potential as a sustainable solution for battery recycling.
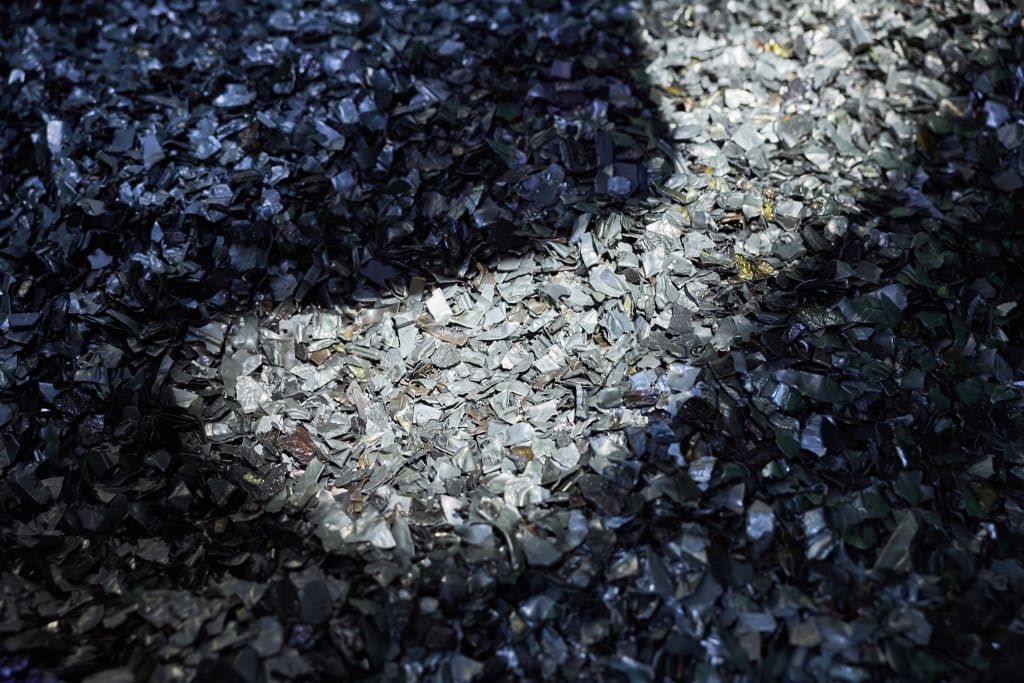
How is regulation and legislation shaping the industry?
As already mentioned, legislation in Europe has been key to the development of the battery recycling industry. The CRMA, alongside new battery regulations, imposes stringent recycling and recovery targets on manufacturers. These measures include mandatory minimum levels of recycled content in new batteries and promote transparency and traceability throughout the supply chain. Such regulations not only ensure responsibly sourced materials but also stimulate demand for recycled battery components, while strengthening recycling infrastructure across the EU.
In comparison to the EU, other regions lack comprehensive legislation for lithium-ion battery life cycle management. For example, the US currently has no federal legislation governing the life cycle of these batteries. However, several states such as New Jersey, Pennsylvania, and Illinois have introduced laws providing guidelines for extended producer responsibility (EPR) including EV battery collection, transportation reuse and recycling.
China also faces regulatory gaps in lithium-ion battery recycling. On one hand, the lack of stringent regulations has, to some extent, facilitated capacity development in the sector. On the other hand, it has hindered broader expansion. Since 2018, China has classified black mass as hazardous waste, banning its import. This restriction has limited the potential volume of black mass available in the domestic recycling market. However, recently the government released its proposed black mass standards that may allow the import of black mass into the country.
Recognising the need to secure critical battery raw materials, the Chinese government is considering easing restrictions on black mass imports. Proposed changes in the coming year aim to relax import rules and provide specific classifications for black mass.
In 2019 the Chinese government enacted legislation for “whitelist” or “state approved” recycling companies. In 2024 a draft of revised version was introduced, which aims to enhance control over the health of recycling operations. The revised whitelist introduced more stringent requirements including lithium recovery rate, environmental standards, and utilisation rates.
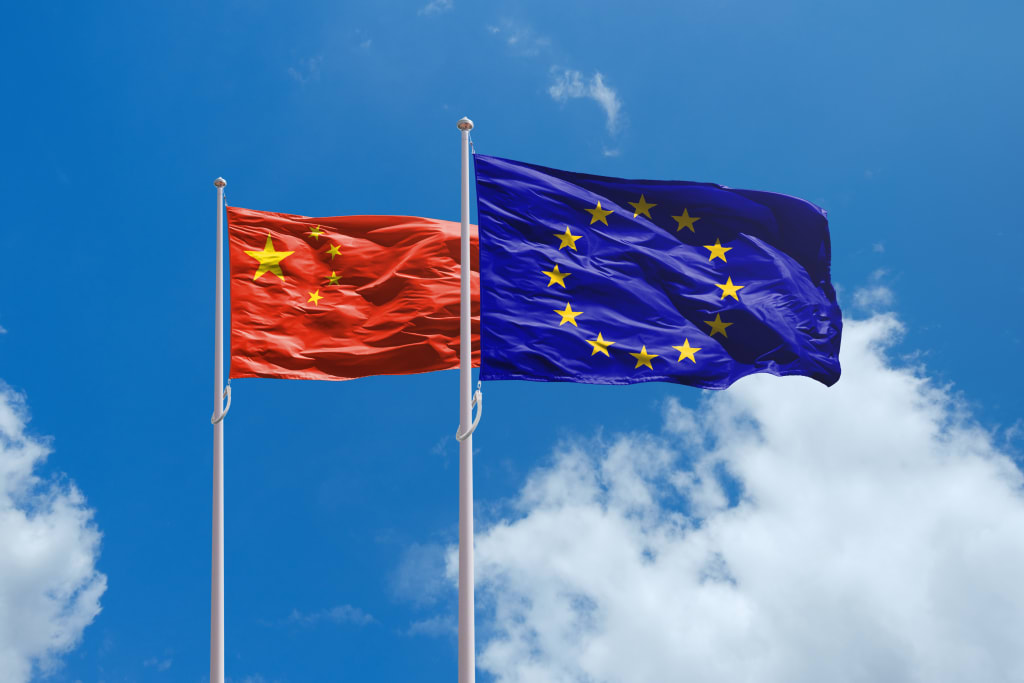
What are the main challenges?
As the recycling industry evolves and matures, players are facing multiple challenges. A key issue companies face is financing, as the industry remains in its nascency revenues remain low, meaning many players are loss making. As these players work on developing technology, expanding processing capacity, and forging partnerships, they remain heavily reliant on equity and debt financing. Although the battery recycling industry is projected to grow significantly through to 2040, several challenges must be addressed to realise this potential. End-of-life EV batteries are expected to become a major feedstock source only after 2030, securing feedstock is key to achieving profitability. Currently, the industry relies predominantly on gigafactory scrap. While this supports technology testing and development, it does not provide substantial revenue opportunities. Companies must carefully manage their resources to avoid depleting their capital before they reach a stage where strong revenues can be realised. Additionally, fluctuations in raw material prices have a significant impact on recycling companies. When raw material prices fall, the income from selling black mass or refined battery materials decreases, further, eroding already tight profit margins.
Conclusion
The lithium-ion battery recycling market is on the verge of significant growth, propelled by rising EV adoption, legislative mandates, and technological advancements in recycling processes. Currently, hydrometallurgy is the preferred technology due to its efficiency in recovering a wide range of metals, while direct recycling presents promising potential for future innovations. The expansion of battery recycling capacity, particularly in China, Europe, and North America, is vital to meet the anticipated demand by 2030.
As sustainability and resource security become increasingly important, lithium-ion battery recycling will play a critical role in establishing a circular economy for essential materials. With supportive legislation, increased funding, and ongoing technological advancements, lithium-ion battery recycling is set to become a cornerstone of the global transition toward cleaner and more sustainable energy solutions.