The battery recycling process is one that has evolved rapidly in recent years alongside increasingly electrified vehicle sales. With EV sales forecast to reach 44 million units by 2030, battery recycling will become a key industry ensuring circularity of materials. Battery recycling largely revolves around three distinct processes, each utilising different technologies: pyrometallurgy, hydrometallurgy, and direct recycling.
This article will run through each of these battery recycling processes including what they are, the challenges and advantages of each and provide an overview of the current global recycling market.
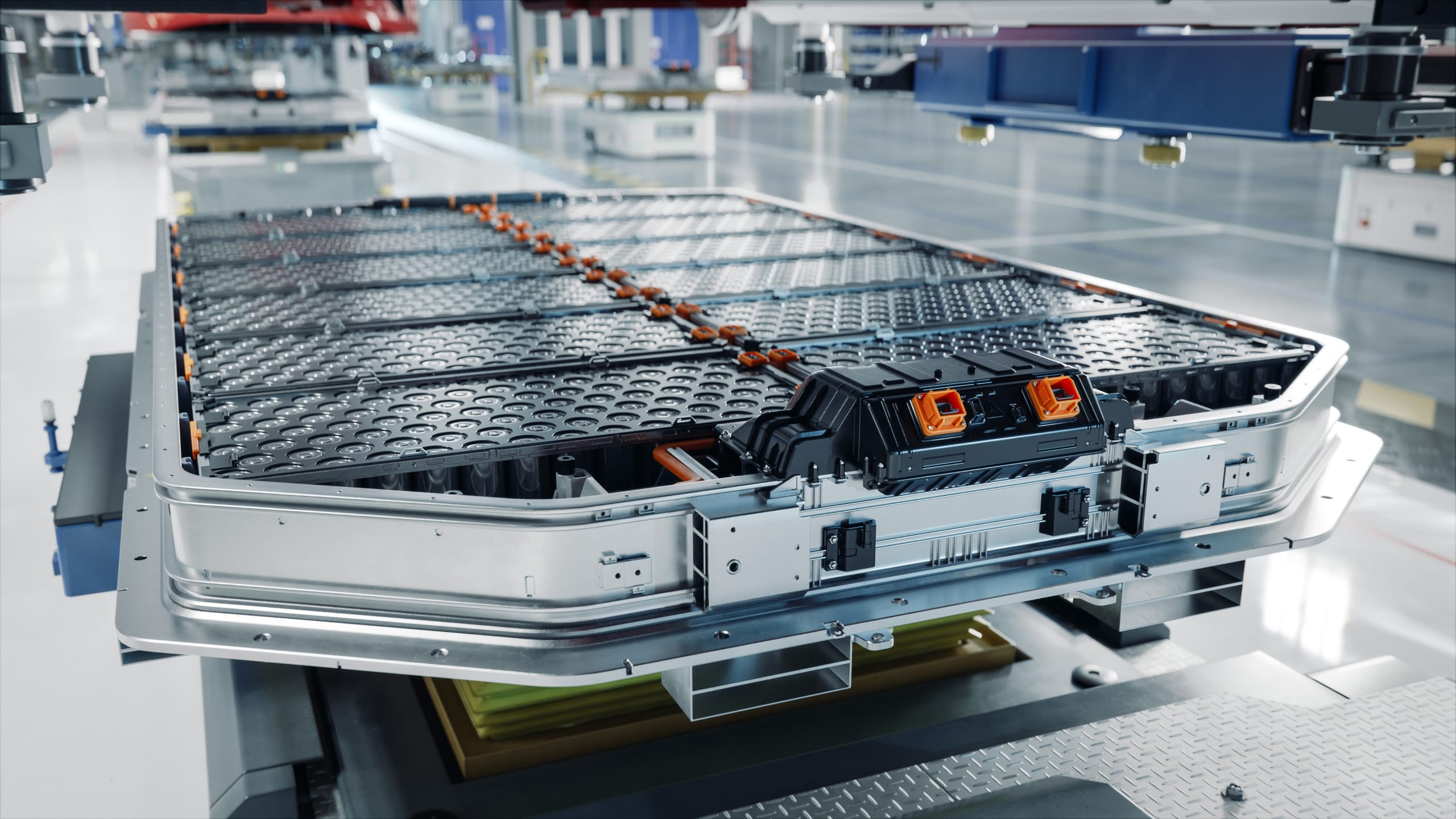
The battery recycling process using pyrometallurgy
Pyrometallurgy involves utilising high temperatures to separate and purify metals from batteries. The process begins with an initial thermal treatment at temperatures ranging from 140°C to 500°C to remove volatile substances such as electrolytes or solvents. Following this, the materials undergo smelting at temperatures between 1400°C and 1700°C. This results in the production of cobalt, copper, and nickel alloys, along with a slag containing lithium and aluminium oxides. These products are then refined further using leaching and solvent extraction techniques to achieve the desired purity.
What are some advantages to the battery recycling process using pyrometallurgy?
The primary advantage of pyrometallurgy is its capability to process mixed waste streams with minimal sensitivity to the origin and composition of the materials. Additionally, the process is relatively straightforward compared to hydrometallurgy and direct recycling. This method benefits from shorter reaction times and lower consumption of concentrated acids.
What are the challenges to the battery recycling process using pyrometallurgy?
During the heating process, materials such as plastics and graphite from the anode and electrolyte are lost through combustion. These are recoverable materials , so their loss leads to a lower recovery rate of critical components.
Another disadvantage is its high energy requirements and substantial emissions of carbon dioxide and toxic gases. However, some companies are overcoming these issues by using integrated chambers, which also leads to decreased energy consumption.
Pyrometallurgy often results in the loss of most lithium and manganese, as they form in the slag or vaporise . To improve economic viability and prevent material loss, pre-treatment is sometimes used to remove some lithium and manganese before heating. Alternatively, further refining of the slag can recover these materials, thereby enhancing economic viability.
The battery recycling process using hydrometallurgy
Hydrometallurgy utilises leaching agents, such as inorganic and organic acids or biological agents, to dissolve metals from end-of-life (EoL) batteries into a solution from which they can be separated and recovered. This method can achieve a recovery rate of over 98% for copper, nickel, and lithium.
The process begins with a black mass creation step where batteries are shredded or crushed into the smaller parts. From here, the process separates valuable materials from other components, resulting in several final products: plastics, scrap metal, and black mass—a high-value commodity containing cobalt, nickel, manganese, and lithium.
The black mass is then further purified and refined through multiple steps to produce battery-grade materials that can re-enter the battery supply chain.
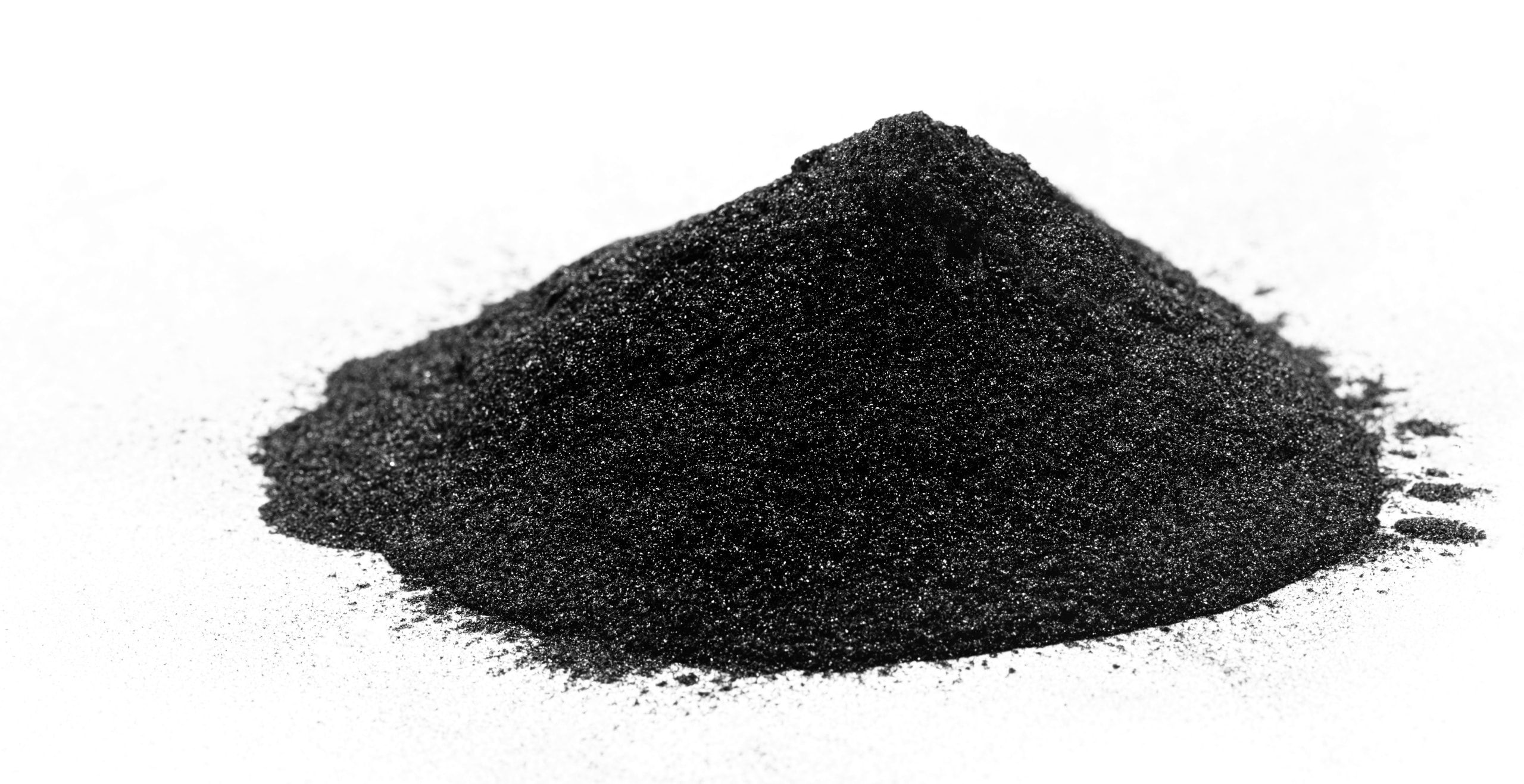
What are the advantages to using hydrometallurgy?
The main advantage of hydrometallurgy is that it results in a better recovery rate and yield of recovered metals, at a purity that means they can re-enter the battery supply chain. Additionally, the process requires less energy and has a lower carbon footprint compared to pyrometallurgy techniques.
What are the challenges to using hydrometallurgy?
Challenges for the hydrometallurgy process primarily revolve around environmental hazards. The release of volatile organic compounds and corrosive hydrogen fluoride poses significant safety and environmental concerns. There is a risk of chemicals seeping into the ground, leading to wastewater pollution and hazardous residues entering the environment. However, many companies using hydrometallurgy employ wastewater treatment processes to reduce the risks of pollutants such as heavy metals leaching out into the environment.
Additionally, the process faces difficulties in handling different battery sizes and chemistries, which can complicate the recovery and purification steps.
The battery recycling process using direct recycling
Direct recycling is typically more straightforward and energy-efficient compared to hydro- and pyro- processes. It involves physically disassembling the battery to separate and recover components, with a particular focus on retaining the valuable cathode material.
This process maintains the functional cathode structure, such as supplementing lithium salts into lithium-deficient cathode materials to maintain or enhance performance. Additionally, regenerating anode materials can further improve the efficiency and sustainability of the recycling process. These cathodes and anodes can then be put back into new batteries.
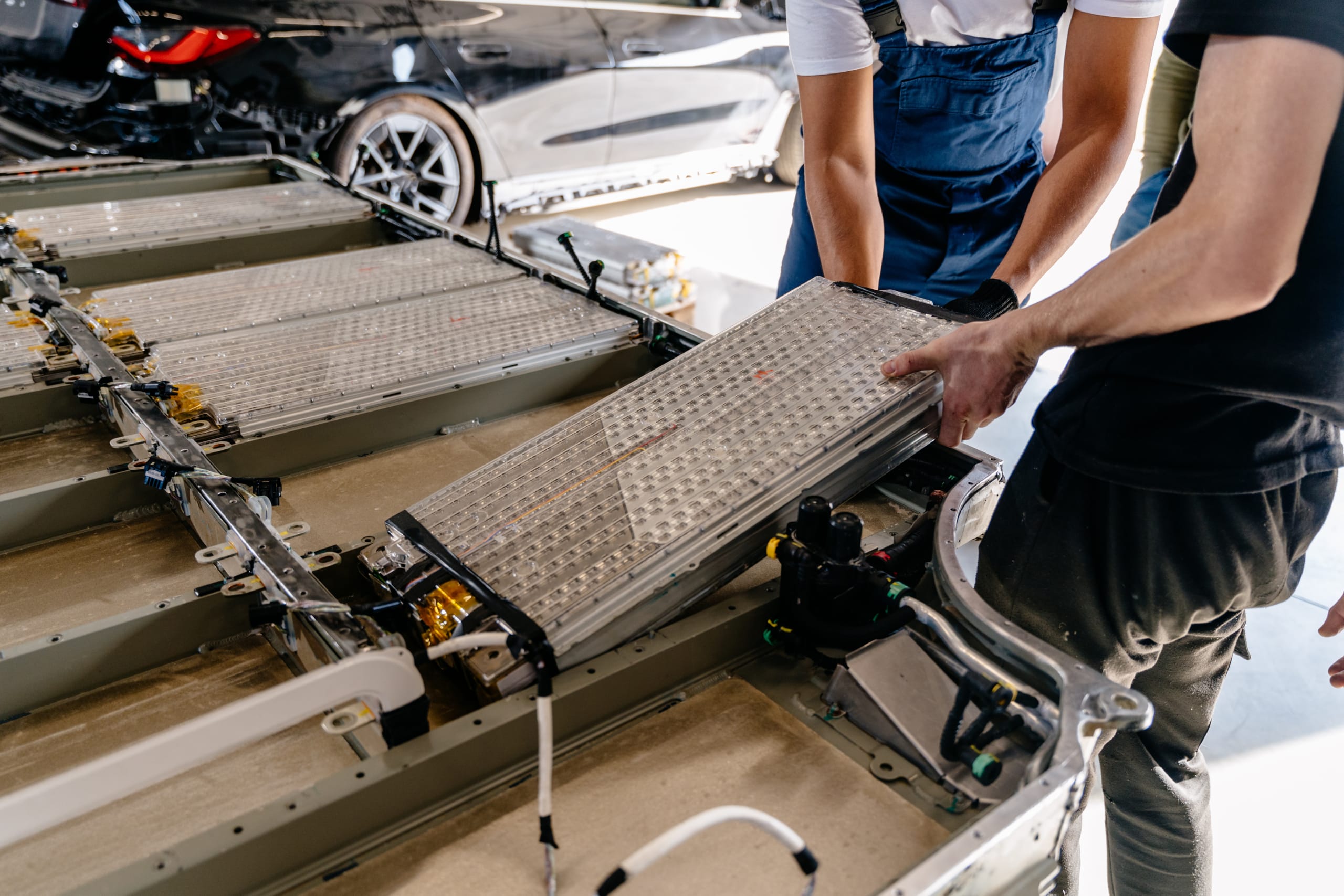
What are the advantages to using direct recycling?
Direct recycling preserves the original battery structure, thus retaining its economic value. It also reduces environmental impact compared to traditional methods that involve harsh chemicals. With fewer downstream processing steps, direct recycling decreases energy consumption and minimises yield loss. Moreover, it results in higher-quality materials with fewer impurities, enhancing overall material quality.
What are the challenges to using direct recycling?
Direct recycling technology for EV batteries is less developed compared to pyrometallurgy and hydrometallurgy. The lack of a well-established commercial industry necessitates optimisation for scalability. Currently, the process is labour intensive, which increases overall costs and hinders the efficiency of the process.
While direct recycling offers substantial benefits, such as economic retention and environmental friendliness, overcoming technological immaturity and scaling challenges are hurdles to its widespread adoption.
Current market dynamics
The battery recycling process used most dominantly in the market is hydrometallurgy, accounting for over 95% of the capacity online currently. The remaining 5% comes from a combination of hydro- and pyrometallurgy, pyrometallurgy alone, and direct recycling.
Whilst battery recycling capacity is being built out, most facilities are currently using production scraps from gigafactories. We expect end-of-life EV batteries to become the main feedstock after 2030.
More information
Rho Motion provides comprehensive, in-depth market analysis on EV and battery recycling markets. For more information about the recycling market and industry trends see our Battery Recycling Quarterly Outlook or Battery Recycling Capacity Database.
For more information on the UK recycling industry see Faraday’s research here.