Introduction
Although they have not enjoyed as much limelight as batteries, electric motors, specifically electric vehicle motors (EV motors) are just as crucial to the electric revolution. EV motors sit at the heart of electric vehicles, converting electricity supplied by the batteries into mechanical energy which propels the vehicle. Besides being cleaner than internal combustion engine (ICE) in terms of emissions, EV motors have a better energy conversion efficiency, making them ideal for the electric energy transition. We have covered the topic of EV motors at Rho Motion for about 3.5 years. Our products have since expanded to cover vehicle platforms, semiconductors, and more recently, autonomous driving. Here, we will delve into the history of EV motors, their types, market landscape, key players and manufacturers, current market challenges, and outlook. We will also take a look at semiconductors, which are increasingly becoming an important part of EVs as the market trends towards increasing automation.
History of EV motors
Advent
Electric motors are part of our everyday life and can be found in so many things around us. Electric motors in vehicles are not a new phenomenon; the first electric motor was developed in the early 1800s. In 1828, Hungarian engineer Ányos Jedlik created a small-scale electric motor, while in 1834, American inventor Thomas Davenport developed a similar device. However, these early prototypes were not practical for powering vehicles due to limitations in battery technology.
The history of EV motors is intertwined with the history of electric vehicles. The first practical EVs emerged in the late 19th century. In 1837, Robert Davidson of Scotland built an electric-powered vehicle, and by 1884, Thomas Parker in England designed one of the first commercially available electric cars. These early electric cars were quieter, cleaner, and easier to start compared to ICE vehicles, which required hand-cranking. By the turn of the 20th century, electric vehicles, steam engines, and gasoline cars were competing for dominance.
Failure
Despite their early popularity, electric vehicles started to lose ground by the 1920s due to several factors including cheaper energy, longer range, and mass production of ICE vehicles. Consequently, electric vehicles all but disappeared by the mid-20th century. However, the oil crises of the 1970s and growing environmental concerns in the late 20th century led to renewed interest in EVs. The development of new battery technologies, particularly lithium-ion batteries in the 1990s, revitalised the electric motor industry, ultimately leading to the modern EV era.
Revival
The 21st century has seen a resurgence in electric vehicle technology, driven by concerns over climate change, advancements in battery technology, and the push for more sustainable transportation. Electric motors in modern vehicles have become highly efficient, compact, and powerful, enabling EVs to compete with traditional ICE vehicles on both range and performance. Major players such as Tesla, Nissan, and General Motors helped propel EVs into the mainstream.
What constitutes an EV motor?
At its core, an EV motor is made up of 2 to 3 essential parts. The stator, the rotor, and the housing which holds everything together.
Stator: The stator is the stationary part of the motor, consisting of a series of copper wire coils wound around an iron core. When an electric current is introduced into these coils, they generate a magnetic field.
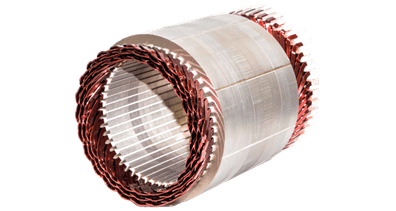
Rotor: The rotor is the rotating part of the electric motor, placed inside or alongside the stator. It is influenced by the magnetic field generated by the stator. This causes it to spin as it tries to align with the stator’s magnetic field. A shaft is typically connected to the rotor, transferring the mechanical power generated by the rotor to an external load such as a vehicle’s wheel or an axle.

Housing: A motor’s external housing or casing protects the internal components (rotor, stator) from environmental factors such as dust, debris, and unwanted moisture. The housing also provides a framework for mounting the motor in different applications and cooling channels required for thermal management of the motor.
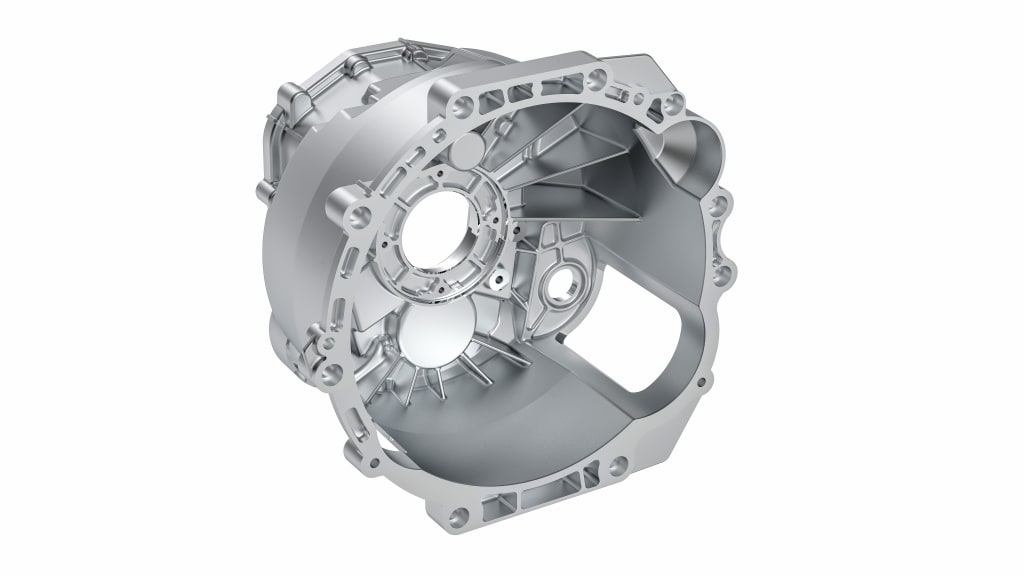
What types of EV motors are there?
There are many different types of electric motors. However, when talking about EV motors, generally this refers to alternating current (AC) motors. These can broadly be divided into two – synchronous and asynchronous (induction) motors.
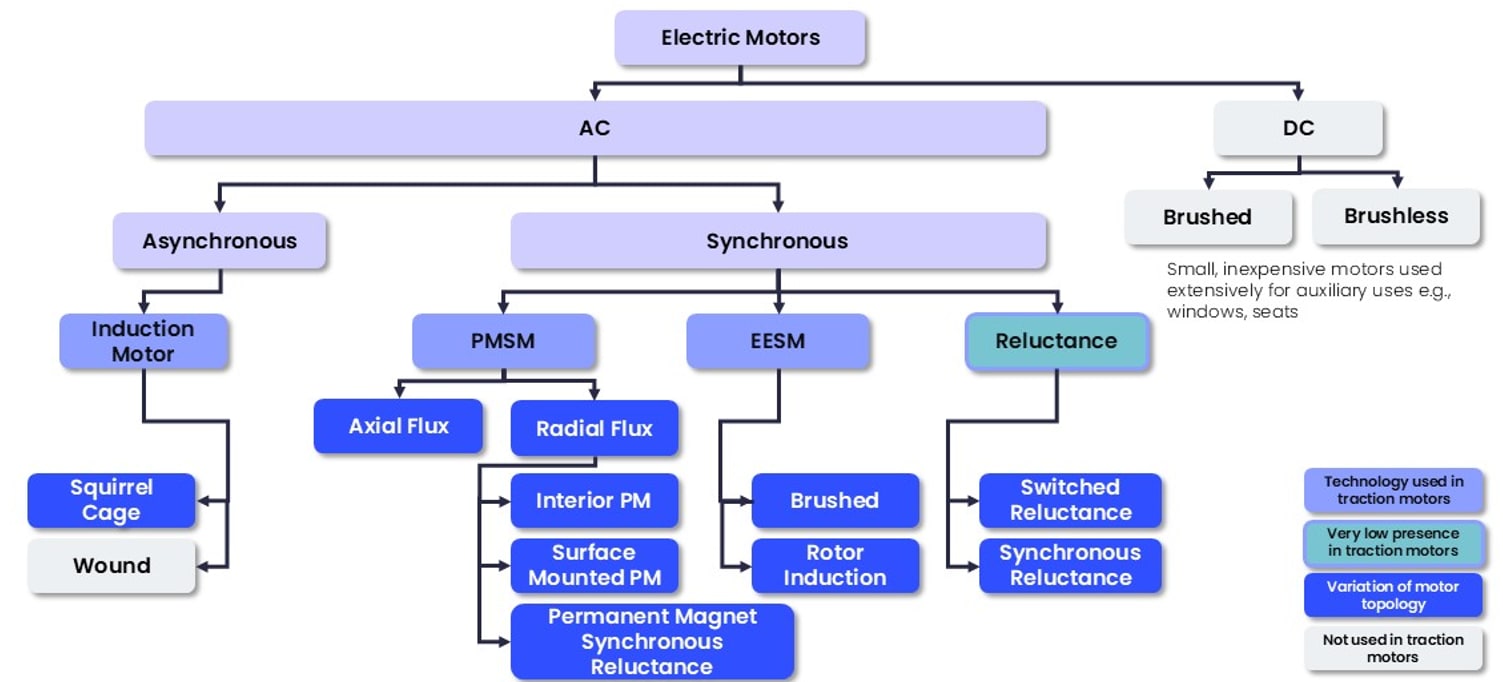
Synchronous motors: A synchronous motor is a type of AC motor that operates at a constant speed which is synchronised and directly proportional to the frequency of the AC power supply. The rotor of a synchronous motor turns at the same speed as the rotating magnetic speed generated by the stator, therefore its speed is independent of the load on the motor.
Asynchronous motors: An asynchronous motor, also known as an induction motor is a type of AC motor in which the rotor does not rotate at the same exact speed as the stator’s magnetic field. It instead operates at a lower speed, creating a relative motion, colloquially called a ‘slip’ between the stator’s rotating magnetic field and the rotor. With increased load, the slip also increases.
At Rho Motion, we focus on four motor types:
Permanent Magnet Synchronous Motors: Permanent Magnet Synchronous Motors or PMSMs are a type of synchronous motors where the rotor is embedded or surface-mounted with permanent magnets (typically made from alloys of rare earth elements neodymium or samarium). PMSMs are particularly advantageous due to their high efficiency, especially at higher loads, and high power density. PMSMs are currently the most popular choice among automakers, steadily enjoying a market share in the 80% – 85% range. PMSMs are also sometimes simply referred to as permanent synchronous motors, PSMs.
Asynchronous/Induction Motors: An induction motor also known as an asynchronous motor is a motor that works based on the principle of electromagnetic induction, where an AC current in the stator produces a magnetic field, which induces a current in the rotor, causing it to rotate. Unlike PMSMs, induction motors do not require an external source of excitation such as a magnet, making them simple and reliable. Tesla was one of the most prominent automakers which used induction motors due to their robustness and efficiency at high speeds. However, in more recent years, Tesla has incorporated PMSMs, especially in its multi-motor configurations, choosing to create an efficient blend of the advantages offered by both motor types.
Externally Excited Synchronous Motors: Externally Excited Synchronous Motors or EESMs are a type of synchronous motor where the rotor’s magnetic field is generated by an external DC power source, as opposed to permanent magnets as is the case with PMSMs, or electromagnetic induction as is the case with induction motors. Like other AC motors, the stator of an EESM is still connected to an AC power source. EESMs are used predominantly in applications focused on rare-earth-free designs. Prominent automakers which use EEMs include BMW, Renault, and Mercedes-Benz.
Axial Flux Motors: Axial flux motors are a type of PMSM that are relatively still in the innovative stage. They differ from other PMSMs in that their magnetic field flows axially, parallel to the rotor axis (hence the name), while other PMSMs are radial flux, meaning their magnetic fields flow radially outward from the centre of the motor. Axial flux motors are extremely compact and lightweight, making them highly power-dense, higher than a radial flux motor of comparable size. Axial flux motors are currently mostly used by high-end performance vehicle brands such as Ferrari and Koenigsegg, and brands which use in-wheel/hub motors like Yangwang (in the U8). Prominent manufacturers of this motor type include YASA Motors, Protean Electric, and Magnax.
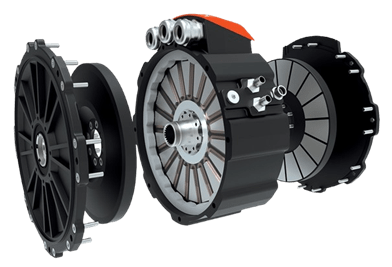
Challenges to PMSMs
As already established, PMSMs currently dominate the EV motor market and are projected to do so for the foreseeable near to medium future. But despite their advantages, there are several drawbacks associated with the use of PMSMs which the EV motor industry is looking to solve.
Cost: Permanent magnets, particularly rare-earth magnets, are the main cost drivers for PMSMs. These magnets are not only materially costly, but also require a complex process to align the magnets within the rotor during assembly, further driving up the cost.
Supply chain security: Mining of rare-earth elements and production of permanent magnets is concentrated in a handful of countries. This constitutes a significant supply chain risk for non-producers as they could find themselves on the wrong end of a geopolitical spat or trade war. In addition, prices for these commodities are often dictated by a few countries, subjecting consumers to price volatility.
Environmental challenges: Rare-earth elements are often found in ores which sometimes contain radioactive elements such as thorium and uranium. As a result, the mining of rare-earth elements poses significant environmental risks, thereby provoking the need for tough environmental regulations and mining restrictions. Naturally occurring rare-earth elements, however, are not radioactive.
What alternatives are there to PMSMs?
While PMSMs have continued to dominate the market, the magnet and production cost problems associated with PMSMs have prompted an industry search for alternatives. Several options are currently being explored.
Magnet-free motors: Induction motors, EESMs, and reluctance motors are all magnet-free motors. However, they have struggled to upset the market lead of PMSMs as PMSMs are often more efficient and power dense.
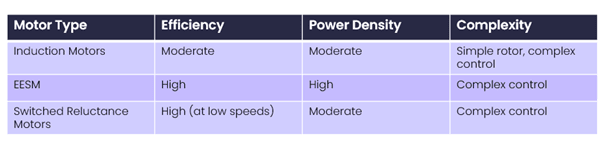
Alt-magnet motors: Another option that is being explored is the use of other magnet types or alternative materials to rare-earth magnets. One such example is ferrite magnets, which are much cheaper to produce than rare-earth magnets. However, ferrite magnets are not as powerful as rare-earth magnets and often cannot work in the same operating temperatures.
Hence, barring a technological or material breakthrough, PMSMs will continue to lead the market for the next few decades.
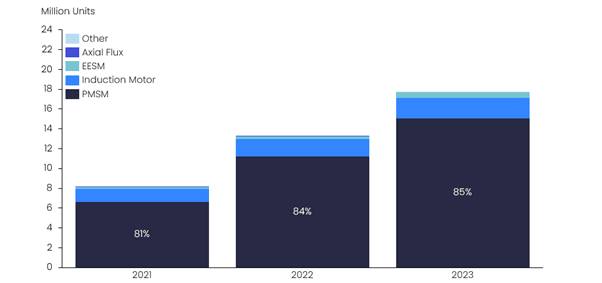
What types of vehicle platforms are used in EVs?
EV motors do not exist in isolation. They are often part of what is known as a vehicle platform. A vehicle platform refers to a set of components, architecture and design elements which form the foundation for (often) multiple vehicle models. For EVs, a vehicle platform consists of a chassis or frame, battery pack, thermal management system, electric motors, power electronics and inverters, suspension and drivetrain layout, and an electrical and software architecture.
Currently, EV platforms come in three main categories.
Skateboard platforms: These are the most common EV platform design types, consisting of a battery pack housed in the vehicle floor, with motors on the axles. This design type maximises interior space and lowers the vehicle centre of gravity, thereby increasing vehicle stability and handling. This platform type is popularly used by Tesla.
Modular platforms: An increasingly popular phenomenon, modular platforms are designed to be flexible across multiple vehicle sizes and types. These platforms allow for different battery sizes, motor configurations, and wheelbases, enabling manufacturers to build sedans, SUVs, and sometimes even vans on the same platform architecture. A popular example of this is Volkswagen’s MEB platform which underpins most of the vehicles in the VW Group. Other automakers such as Ford and VW’s partner ventures with SAIC and FAW in China also use the MEB platform.
Custom: High-performance, particularly, luxury EVs often use custom platforms which are designed for optimal weight distribution, high speeds, and superior handling.
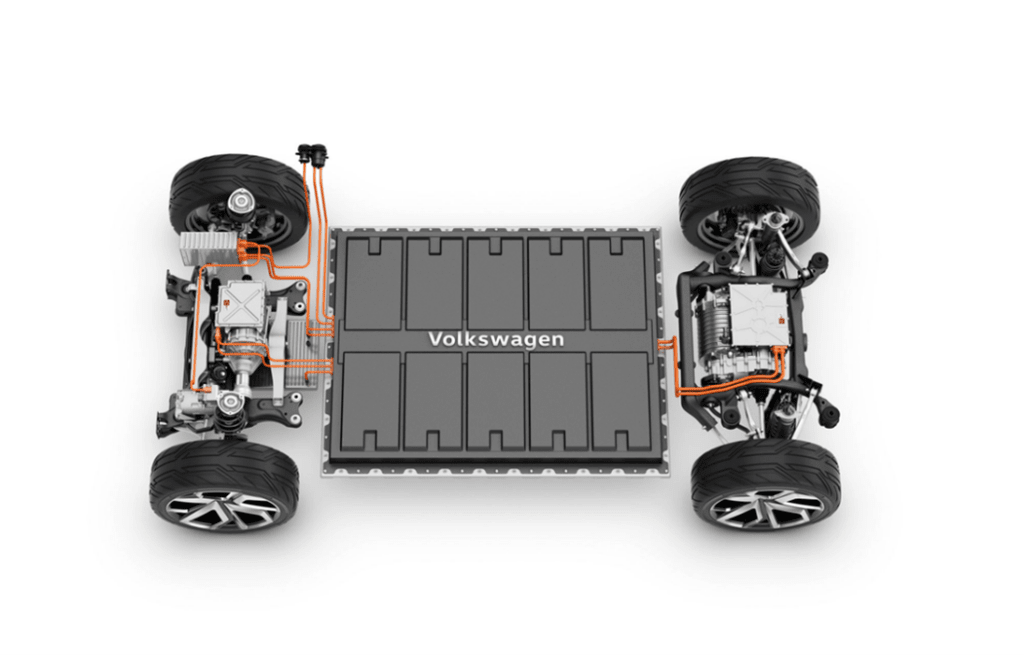
400V vs 800V platforms
Platforms can also be broadly categorised into either 400V or 800V. However, these values are not fixed, but are in fact, a range. A vehicle with an operating voltage within a range of 300 – 500V will fall under the 400V platform category, while a vehicle with an operating voltage between 600 – 900V will fall under the 800V platform category. Currently, most EVs come in 400V platforms but there is increasing interest in 800V platforms as they allow for improved power output and motor performance.
Silicon carbide vs silicon inverters
An electric motor’s inverter is crucial to how the motor functions. The primary function of the inverter is to convert direct current from the vehicle’s battery into alternating current which is required to power the motor. Other functions of the inverter include:
- Regulating motor speed and torque;
- Reversing the direction of current flow for regenerative braking;
- Protecting the motor and battery from overheating, and overcurrent.
Due to rising interest in 800V platforms, silicon carbide (SiC) inverters are becoming more mainstream as they can withstand the higher platform voltage. In addition, SiC inverters have a better thermal tolerance and increased efficiency due to their higher switching speed. While SiC use in traction motors is expected to increase in the future, this will likely be stymied by the limited adoption of 800V platforms. However, SiC inverters are not restricted to 800V platforms. Tesla is a noteworthy example of an OEM that uses SiC inverters in its 400V platform vehicles.
What role do semiconductors play in EVs?
Semiconductors form the backbone of modern electronics, powering everything from smartphones and computers to EVs and advanced industrial systems.
As the demand for intelligent EVs continues to rise, the role of semiconductors in automotive applications has grown exponentially. The integration and volume of semiconductor components directly determine a vehicle’s level of intelligence and functionality.
Semiconductors not only are fundamental to essential systems like microcontroller units (MCUs) that manage vehicle operations but also play a pivotal role in advanced features such as autonomous driving sensors and smart cockpits. Enhancements to the driving experience, such as voice control, human-machine interaction, and augmented reality displays, are increasingly reliant on cutting-edge semiconductor technology.
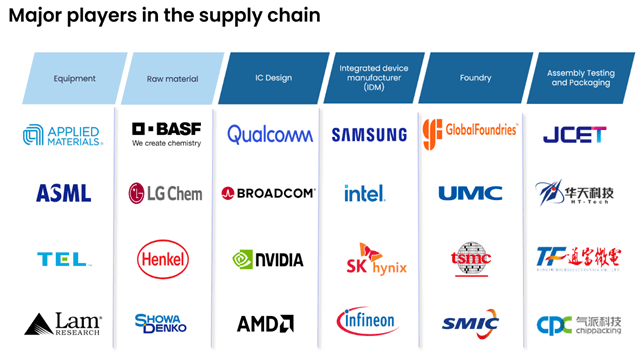
To better understand the automotive semiconductor industry and its challenges, it’s important to first explore the basics of semiconductor production. This foundational knowledge will help readers grasp the complexities of the industry and the challenges it faces.
The semiconductor industry consists of a well-defined value chain, divided into upstream and downstream segments, each with specialised roles and dominant players.
Upstream: Equipment and Raw Materials
The upstream segment of the semiconductor industry encompasses the production of equipment and raw materials essential for chip manufacturing.
- Equipment
Manufacturing advanced semiconductors requires highly sophisticated tools, among which photolithography machines are the most critical. These machines are dominated by companies in Japan and Europe, with ASML, a Dutch company, standing out as the industry leader. ASML’s extreme ultraviolet (EUV) lithography machines are pivotal for the production of the smallest and most advanced semiconductor nodes, setting technological benchmarks for the industry.
- Raw Materials
The production of semiconductor wafers relies on ultrapure silicon, which is primarily supplied by Japanese companies. The stringent purity requirements for silicon wafers act as a significant barrier to entry, restricting competition and solidifying the dominance of a few key suppliers. These materials are critical to ensuring the functionality and reliability of semiconductor chips.
Downstream: Design, Manufacturing, and Assembly
The semiconductor chips are designed, manufactured, and packaged in the downstream sector for various applications.
- IC Design
Integrated circuit (IC) design firms conceptualise and create the blueprints for semiconductor chips. Companies like Qualcomm, NVIDIA, and MediaTek excel in designing chips tailored for specific functions, such as computing, connectivity, or artificial intelligence.
- Integrated Device Manufacturers (IDMs)
Some companies, such as Intel and Samsung, operate as IDMs, combining IC design and manufacturing processes under one roof. This vertical integration allows them to control the entire production process, from design to fabrication.
- Foundries
Pure-play foundries focus exclusively on semiconductor fabrication, producing chips designed by IC design firms. Taiwan Semiconductor Manufacturing Company (TSMC) is the global leader in this space, particularly in advanced process nodes. TSMC’s announcement of 2nm node production by 2025 exemplifies its technological leadership, as these small nodes enable higher performance and energy efficiency in chips.
- Assembly, Testing, and Packaging
After manufacturing, semiconductors undergo assembly, testing, and packaging to ensure quality and functionality. These processes are labour-intensive and often outsourced to regions with lower labour costs, such as Southeast Asia. The ATP phase is crucial for preparing semiconductors for integration into end products like vehicles or consumer electronics.
What are the key challenges facing the automotive semiconductor industry?
The automotive semiconductor sector is experiencing significant challenges, many of which stem from the complexities of transitioning from consumer electronics to automotive applications. These challenges highlight issues in profitability, supply chain reliability, and industry dynamics.
1. Transition challenges: lower margins and longer timelines
Unlike the high-margin consumer electronics market, the automotive value chain is characterised by lower profit margins and stringent safety standards. Developing semiconductors for vehicles often requires extensive simulation and testing, which elongates development timelines. The slower return on investment and increased costs deter some semiconductor manufacturers from prioritizing automotive applications, further complicating supply chain reliability.
2. Struggles of small and medium enterprises (SMEs)
Unlike larger corporations such as TSMC, Intel, or Qualcomm, smaller enterprises prioritise survival over long-term strategic planning. Their focus on cost reduction leaves little room for investment in breakthrough technologies or future-ready solutions. This dynamic creates a disparity in the industry’s growth trajectory, with big players advancing rapidly while smaller firms lag. To be more specific, they face several issues such as:
- Testing and validation costs: Ensuring semiconductors meet automotive-grade standards requires rigorous testing, which becomes more cost-efficient only at large scales. SMEs producing lower volumes struggle to dilute these costs.
- R&D costs: The research and development expenses for advanced integrated circuit (IC) design are immense, often necessitating support from governments or financial institutions. Without sufficient funding, SMEs focus on cost-cutting measures, limiting their capacity for innovation.
- Labor costs: Recruiting and retaining skilled engineers, particularly for cutting-edge fields like IC design, remains expensive and competitive.
3. Challenges in automotive semiconductor design
Automotive semiconductors must meet specific requirements for durability, safety, and reliability that go beyond those of consumer electronics:
- High safety standards: Chips used in vehicles must perform flawlessly under extreme conditions, necessitating stricter manufacturing and testing protocols.
- Cost vs efficiency: While cutting-edge technology is not always necessary, achieving functional efficiency at a lower cost remains a challenge, especially for emerging markets.
4. Broader industry-wide talent shortages and supply chain constraints
The semiconductor industry is grappling with a global shortage of skilled professionals. Developing expertise in specialised areas such as advanced IC design, photolithography, and materials science demands significant investment in education and training, which many regions struggle to implement at scale. This talent gap poses a critical challenge to the industry’s growth and innovation.
Adding to these difficulties is the highly segmented nature of the semiconductor supply chain. Each region dominates specific segments of the chain: equipment production, raw materials, or manufacturing. Attempting to consolidate the entire supply chain domestically, even in the long term, presents significant obstacles. Achieving such integration requires vast investments not only in talent but also in the cutting-edge equipment essential for semiconductor production.
Even for countries or companies that excel in one segment—such as ASML with its dominance in photolithography equipment—challenges persist. For instance, 85% of ASML’s machine components are imported, highlighting the interconnectedness and interdependence within the global supply chain.
These complexities are further exacerbated by geopolitical tensions. Trade restrictions and political disputes threaten to disrupt the fragile supply chain, creating uncertainties in material access, production continuity, and technological development. These vulnerabilities emphasise the urgent need for cooperation and resilience-building in the semiconductor industry.